Asset Integrity
GPS is one of Global Companies, which specialized in operation, maintenance, installation, development, Commissioning and pre-commissioning for the oil and gas, petrochemical, fertilizer, electricity, water and cement sectors, among others. GPS wide range of services includes, but is not limited to, long-term operation and maintenance, overhaul of high-tech plant equipment, and development of plant-specific standard operating and maintenance procedures. Which is known to require a great deal of innovation and many technical approaches.
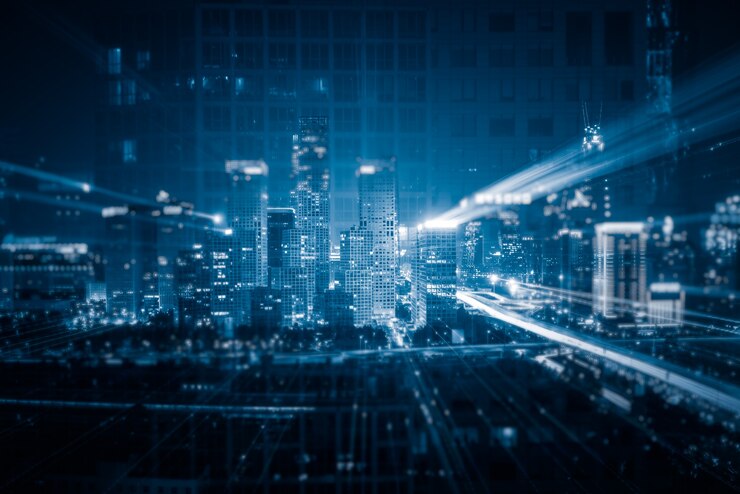
Asset Integrity
The power industry worldwide has been the subject of major reviews and reforms in recent years, which have resulted in changing demands in respect of enhanced safety, reliability, environmental safeguards and commercial competition. In such an environment it is essential that the personnel, the plant and the equipment involved, perform to their optimum levels of capability. Plant & Equipment Reliability System is a maintenance Optimization tool which has a role in providing an effective response to such demands on the industry, by enhancing the effectiveness of operations and maintenance programs.
GPS Reliability Team is leading experts in the oil & Gas field to ensure that plant systems and equipment achieves a consistent and appropriate reliability level to meet the available targets for safe production of all products in line with business objectives.
Reliability and Asset Integrity scope of work can be summarized as follows but not limited to:
- Identification of Potential (High/Medium/Low) Equipment and predict effects on Plant Operations and Production Schedules.
- Development and Implementation of Reliability Strategy for the Plants.
- To liaise with vendors and other parties to develop Strategy and solutions to reliability Problems.
- Contribution in preparation of annual Plans and budgets and monitor cost.
- Contribution in the preparation and management of shutdowns & any other specials activities.
- GPS- Reliability Techniques Experience:
- Criticality Analysis (CA).
- Root Cause Analysis (RCA).
- Failure Mode & Effect Analysis (FMEA).
- Reliability Centered Maintenance (RCM).
- Risk Based Inspection (RBI).
- Key Performance Indicators (KPIs).
Inspection is an important function of any predictive maintenance program. Most of these inspections utilize Non Destructive Tests (NDT) which is a group of very specialized technical procedures to provide information about the condition of materials or components.
Inspection can reveal the presence of flaws which can be evaluated against accept/reject criteria.
There are many recognized and widely used inspection techniques.
GPS can professionally perform many of them such as:
- In-Line Inspection Development & Implementation
- Fitness- for Purpose Assessments
- Risk Management / Pipeline Maintenance Prioritization Programs / Due Diligence Assist
- Stress Corrosion Cracking Management (SCC)
- Regulatory Compliance
- Field Evaluation/Defect Assessment
- Failure Analysis & Remediation Program
- Risk assessment and safety evaluation
- Non Destructive Tests – NDT (PT, RT, UT, MT & ET)